FRP Round Shape Cooling Towers:
We are expertise in manufacturing and supplying FRP Round Shape Cooling Towers in bulk requirement. FRP Round Shape Cooling Tower coupled with the ability to provide cooling tower installation, maintenance and repairing services makes us an undisputed leader in the arena. Round Shape FRP (Fibre glass Reinforced Plastic) Cooling Towers also called as Bottle Shape Cooling Towers. The casing and basins are designed to withstand severe vibration, high wind load and to resist corrosion. The FRP Round shape Cooling Towers consists of Honey comb PVC fills and eliminators in a design that maximizes economy and efficiency and directly driven fan and Motor ‘Minimum drift Losses. Uniform distribution of hot water by rotating arm sprinkler. Hot dipped Galvanized hardware to withstand wind forces. The round shape makes possible to provide maximum cooling efficiency in minimum plan area with lower energy consumption.
Image:
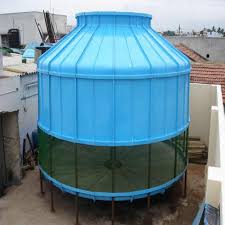
Process;
FRP Round shape cooling tower design incorporates hot water inlet at the bottom collection sump circulated vertically to the mechanical rotary sprinkler located above the fill media. The inlet water pressure rotates the sprinkler, having extended arm pipes with orifices to disperse water uniformly over the fill media. The fan directly coupled to the motor, during operations takes away the heat by induced draft mechanism. Air is drawn from the lower air intake area & is induced to travel through the fill media thus taking away the latent heat from the water passing through the fill media. Portion of water evaporated, removes the heat from the remaining water. The warm moist air is drawn through the fan deck is discharged to the atmosphere. Cold water, collected at the collection sump, is re-circulated to the source. The distinguishing features of our product are compact design Honey comb type PVC fills, with varying flute sizes, to provide maximum contact surface area and heat transfer surface per unit volume.
Benefits:
- High Strength
- Chemical Resistance
- Part Consolidation
- Durability
- Fatigue Life
- Incombustible
- Acceptable cost leave
Advantages:
- Close approach
- Greater thermal efficiency
- Higher energy saving
- Ease of maintenance
- Economy of initial as well as running cost with longer life
- Turnkey solution.
Features:
- Environment friendly
- Long service life
- Maintenance free
- Thermal efficiency
- High efficient
- Rigid structure
- Flawless performance
Applications:
- Air Conditioning Plant
- D G Set / Turbines
- Injection Moulding / Plastic industries
- Induction furnaces / steel plant
- Automobile industries
- Chemical and petrochemical industry
- Paper mill and sugar mill
- Refinery and Fertilizer industry