Industrial Pressure vessel:
We are manufacturing the industrial Pressure Vessels that are manufactured using premium grade steel. Industrial pressure vessels are sourced from registered manufacturers, who make sure to manufacture the entire range as per the clients’ specifications. Furthermore, our pressure vessels are known for withstanding extreme temperature conditions in various industrial applications. industrial pressure vessel is manufactured using premium grade stainless steel that is sourced from known and verified dealers. These Stainless Steel Pressure Vessel can also be customized as per the customer’s requirement and are presented at the best rates in the industry.
Process:
Industrial pressure vessels are made of steel. To manufacture a cylindrical or spherical pressure vessel, rolled and possibly forged parts would have to be welded together. Some mechanical properties of steel achieved by rolling or forging, could be adversely affected by welding, unless special precautions are taken. In addition to adequate mechanical strength, current standards dictate the use of steel with a high impact resistance, especially for vessels used in low temperatures. In applications where carbon steel would suffer corrosion, special corrosion resistant material should also be used. Industrial pressure vessels are made of composite materials, such as filament wound composite using carbon fibre held in place with a polymer. Due to the very high tensile strength of carbon fibre these vessels can be very light, but are much more difficult to manufacture. The composite material may be wound around a metal liner, forming a composite overwrapped pressure vessel.
Image:
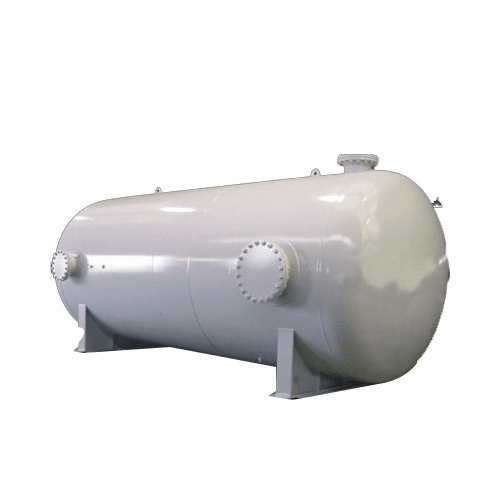
Features:
- 25 ml to 100 litres. size
- Pressures up to 350 bar (4500 psi) & temperatures up to 500°C
- Available in different Materials of Construction (MOC) like SS-316, SS-316L, hostelry B/C, model, Nickel, Titanium, Tantalum, Zirconium
- Ex-proof / CE / PED / ASME certified systems on request
- Fully automated PC controlled high pressure system / pilot plant to continuously monitor, control & record various parameters.
6.High impact resistance
7.Corrosion resistant
8.Abrasion resistance
9.High tensile strength.
Advantages:
- Low investment, operation and maintenance costs.
- Highly efficient heat transfer (K- values on average 3-5 times higher than in case of bare-tube heat exchangers).
- Asymmetrical flow gap available for the most cost effective solution.
- Use of smallest temperature difference </= 1°C
- Up to 75% less space required.
- Self-cleaning effect due to highly turbulent flow behaviour
- Future additional capacity is possible by fitting extra heat transfer plates
- Double gasket with leak groove gives high safety with regards to media mixing.
- Easy to open/clean
- Low operating weight/ low liquid content.
Applications:
- Acid digestion
- Static, loop, electrochemical, corrosion studies
- Supercritical fluid extraction
- Hydrogen induced dis bonding tests
- Soaking of diamonds / precious stones.