Water Based Heat Exchangers:
Water based heat exchangers are designed according to customers’ requirements and assure exact compliance with their performance specifications. Our finned systems enhance heat exchange to the tube system and allow low material usage without performance loss. Tooling flexibility allows each system to be adjusted with its tube banks side by side or on top of each other, offers options of meeting extreme customer demands. Our many official approvals and certifications allow us to design and manufacture water based heat exchangers for many and various applications.
Process:
Principles of water based heat exchangers are manufacture of assemblies which included brazed components and in which nickel/chromium-based filler metals are used wherein the manufactured assemblies are characterized by low leaching rates of nickel in water and water-based fluids, are disclosed. More specifically, there are disclosed methods for the manufacture of a heat exchanger or other assembly which method includes a brazing step, as well as a post-brazing conditioning step for treating the heat exchanger or other assembly. The manufactured heat exchangers and other assemblies are particularly useful in the handling of materials intended for human consumption such as water, beverages or food as the manufactured heat exchangers or other assemblies are characterized by reduced leaching rates of nickel into fluids passed through the heat exchanger.
Image:
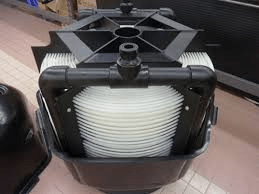
Materials:
- Standard: CuDHP smooth
- CuDHP internally grooved (only for refrigerant operation)
- CuDHP pertinent
- CuDHP thick- wall tube
- Aluminium fins
- Copper fins
- pre- lacquered fins
- hydrophilic fins
- Copper
- Stainless Steel (1.4301, 1.4571)
- AlMg3
Features:
- The closed circuit medium is accessible in its entirety
- The heat exchanger is at low level allowing ease of routine maintenance
- Plates are manufactured in 304 or 316 stainless steel
- Facility to add additional plates for extended cooling surface
- Reduce exchanger mean temperature differences (MTD’s)
- Minimize cooling water consumption
- Debottleneck summertime limited condensers
- Reduce column operating pressure and increase capacity.
Applications:
- Liquid-to-liquid
- Cryogenic
- High pressure
- Clean steam generators
- Blow down
- Natural gas heaters
- Vent condensers
- Mechanical seal coolers
- Compressor inter/after coolers
- Supercritical fluid
- Feed water preheaters
- Lethal service
- Steam or process fluid vaporizers
- Boiler or process sample coolers